Insight Micro-Rotor Squelette calls on an area of craftsmanship for which Romain Gauthier and his team have been heralded since the birth of the brand in 2005: hand-finishing.
For each Insight Micro-Rotor Squelette movement features as many as 250 hours devoted to the anglage alone, that’s to say the bevelling, softening, smoothing and polishing by hand of the bridges and mainplate, in an extraordinary demonstration of watchmaking artistry.
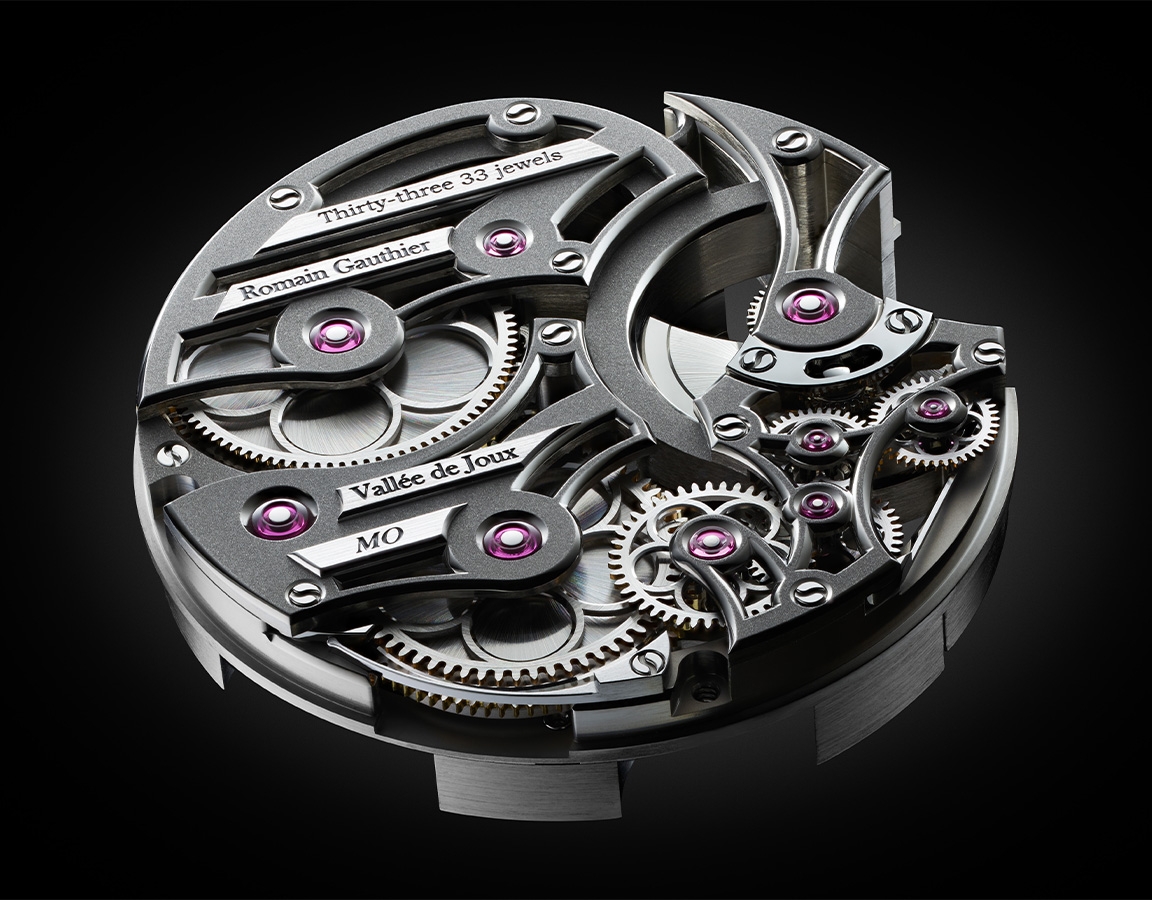
Material decisions
Romain’s design for an openworked Insight Micro-Rotor entailed skeletonising the mainplate and eight bridges. At the thicknesses he envisaged, skeletonised brass bridges might not have held up. But Grade 5 titanium would offer the requisite strength, lightness, ability to look good naturally, and ability to undergo anglage.
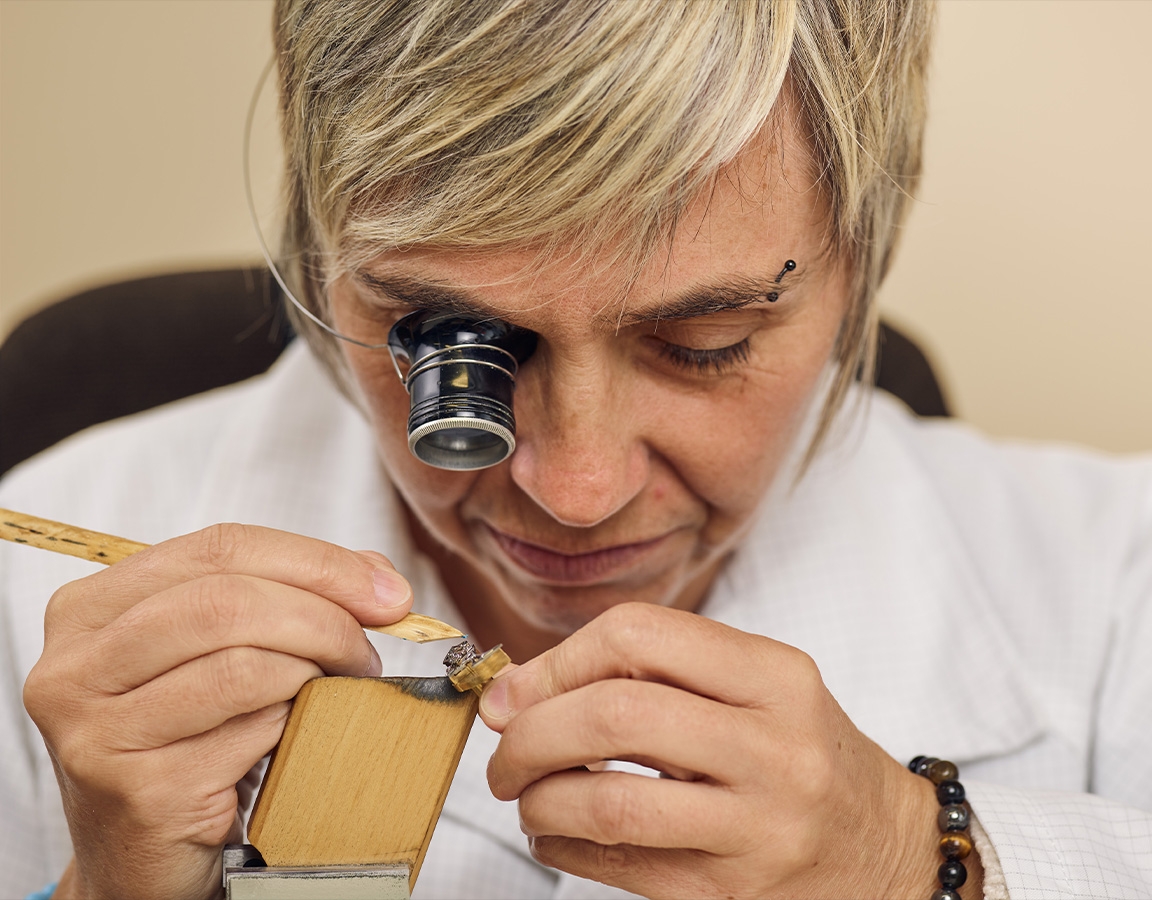
Anglage in a nutshell
Anglage beautifies the component by creating a polished bevel between its surface and flanks, one which catches the light and the eye. The angleur or angleuse creates a bevel using a steel file, softens and smooths the material with degussit then a series of buffs with emery-paper tip, before polishing the bevel using the woody stem of the gentian plant with diamond paste.

A test of talent
Insight Micro-Rotor Squelette put the talents of the Romain Gauthier anglage team to the test. The complexity of the shapes created by the skeletonization – featuring no fewer than 156 angles, the majority of them sharp, internal angles – made it tricky for these artisans to access, while limiting the scope of movement that their hands can make.
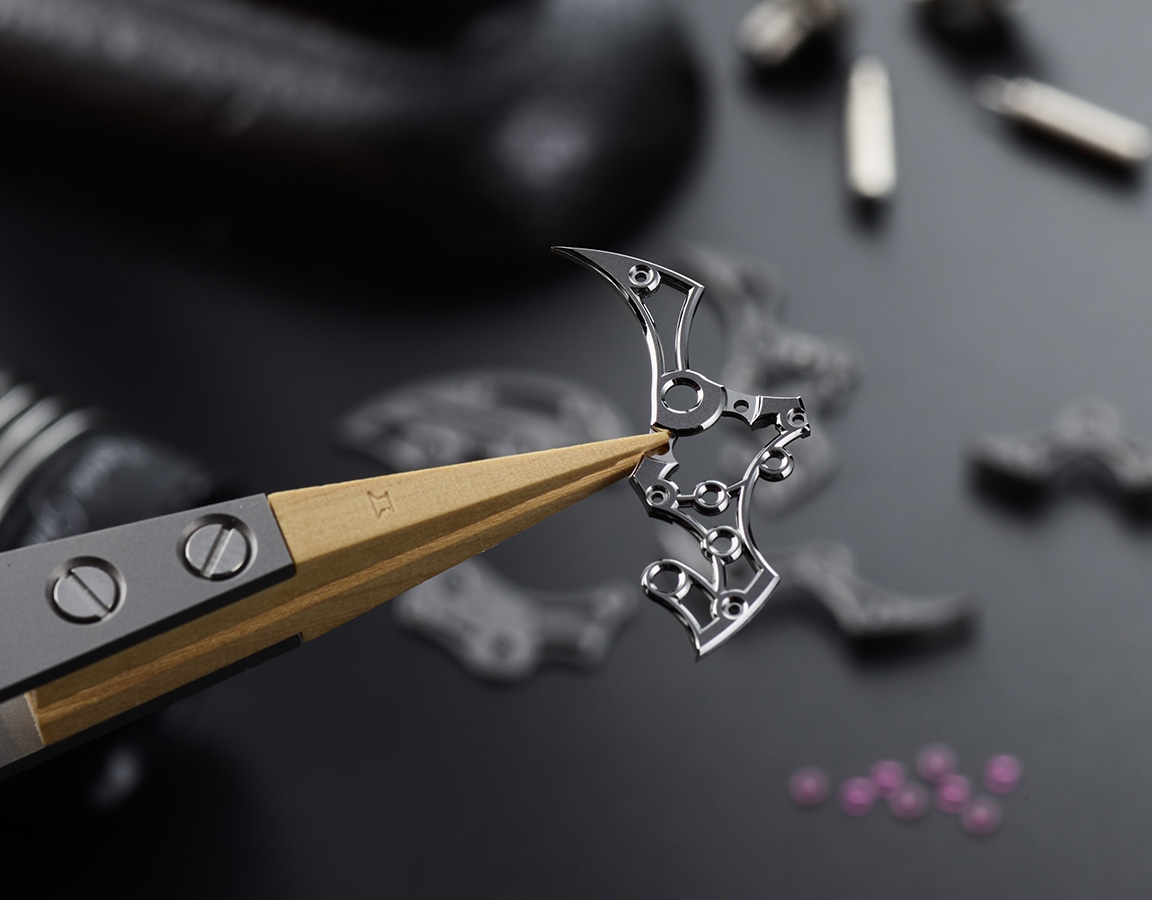
Challenge of titanium
“When working with titanium, each of the bevelling, softening, smoothing and polishing stages take far longer,” says Sylvie Devaux, Head of Anglage at Manufacture Romain Gauthier. “You can come across micro-grains in the titanium that detach, leaving you with tiny spots. The only solution is to go back over the angle all again.”
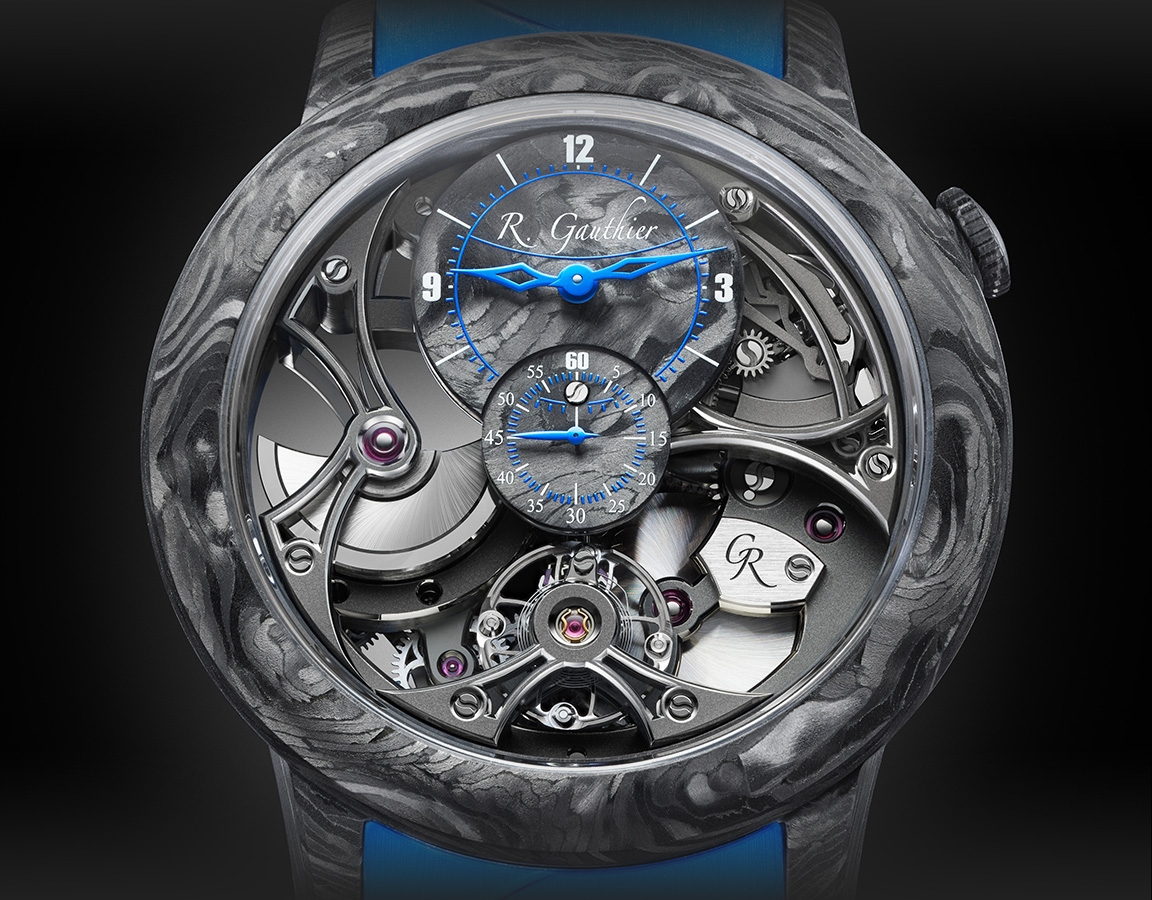
Off-the-scale hand-finishing
It takes one Romain Gauthier anglage specialist 250 hours to bevel, soften, smooth and polish by hand the natural titanium mainplate and seven bridges. When you add up all the hours devoted to decorating the entire movement by hand – including anglage, hand-frosting, polishing countersinks, circular graining, straight graining and snailing – it comes to over 350 hours of work!
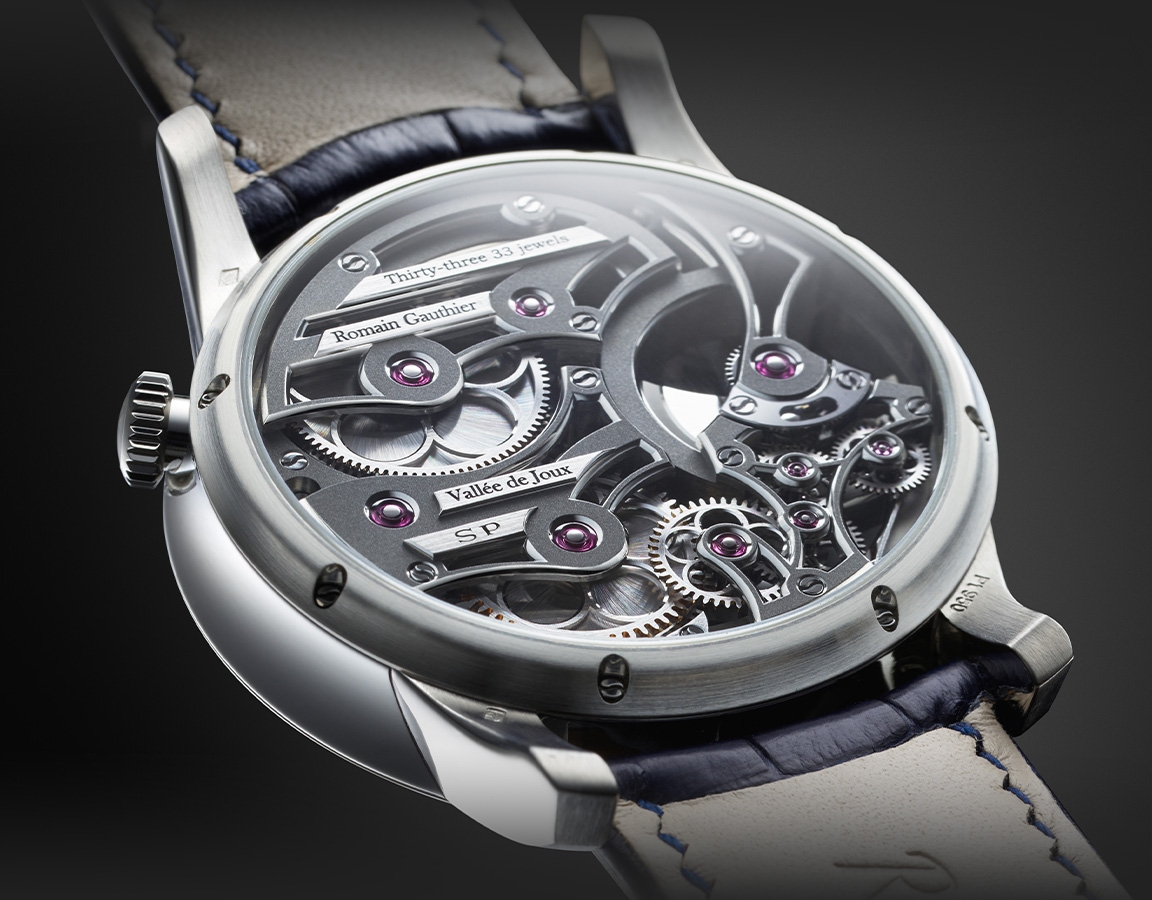
Like a marathon
Sylvie Devaux concludes: “Performing the anglage for one Insight Micro-Rotor Squelette is a real test of mental stamina. For a month and a half, 8 hours a day, you have to really be in the zone, concentrating so hard. It is like a marathon. You have to approach it angle by angle, component by component, until you finally reach the finish line and get that feeling of accomplishment.”
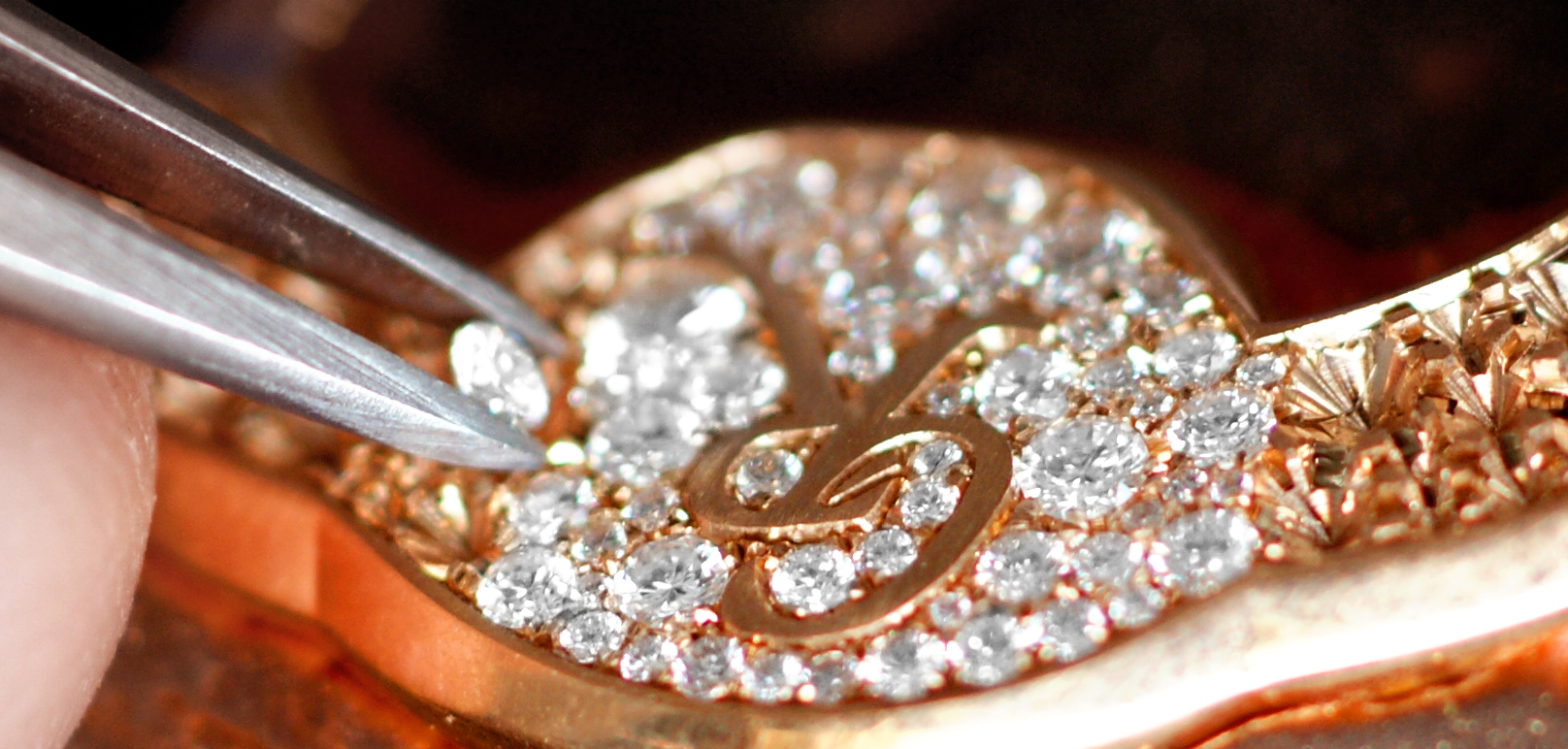